From the previous post, i have been working on the idea of bistable joints. As you can see that Prototype #5 for the first testing of the idea. I have tried a few others meanwhile.
In aluminium In MS. it is too heavy, but the concept works. A blind rivet limits the 2 elements from going beyond the extreme positions Some shapes… Same piece, but locked in a different shape. Another shape.
These worked, but then they didn’t. Here are the challenges:
- The joints broke with the tension and weight. Learning – don’t use pop rivets for joints!!!!
- Aluminium is better than MS, because it makes the structure so much lighter. However welding in aluminium is not easy.
- The joints and structure flexes quite a bit, and so it does not maintain shape under the tensioning system. The whole point is lost if you tension the steel cable but then the elements flex it out. No wonder it could not hold its own weight.
So, after a long gap of thought paralysis (1 year) I reattempted what i call the 16th Prototype. It is made out of cylinders, rather than sheet metal. Here’s why:
- Cyclinders look nicer than industrial looking sheet metal works. Note that this is an important feature if it has to be used as a home furniture!
- Cylinders are available, and common. One does not need to resort to laser cut pieces and machinery in this way, thus making the design more accessible as an open-source design.
A technique of bistable elements mechanism was invented using cylinders and regular fabrication workshop. Illustrated here.
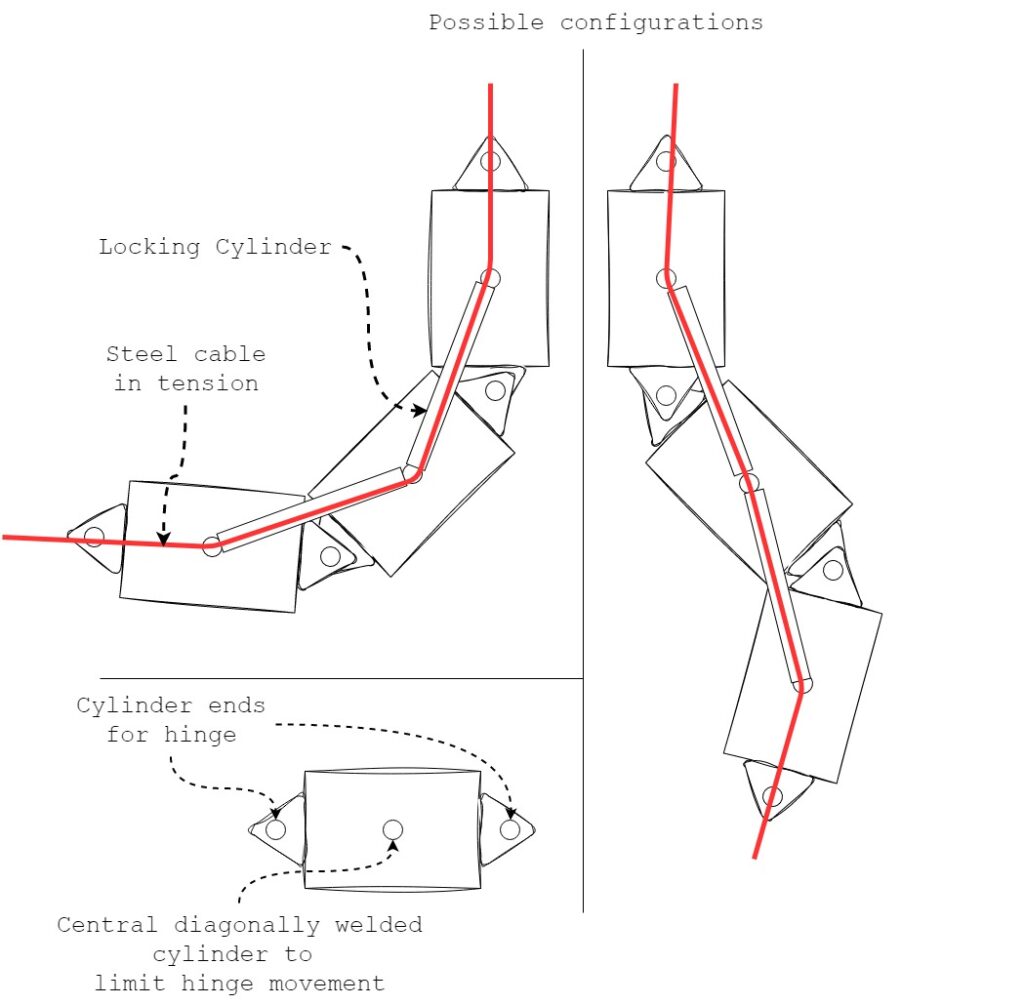
Each bistable section has 4 features:
- 2 main cylinders,
- A hinge comprising of extended edges of the 2 main cyclinder. Note that there is no pin passing through to the other side, so central portion of the hinge piece is free.
- Another cylinder of small diameter diagonally welded into the main cyclinders. There is also a hole at the center of the cylinder’s length through which the steel cable passes.
- A 4th cylinder through which the steel cable passes and which limits the bistable system in either extremes of the movement.
Here is how it looks after assembly:
Failures
- Each main cylinder has 2 different axes for the hinges at both the ends. This allows for the stand to take on any shape in 3D. However, this makes it difficult for the central locking cylinder to lock on to the diametrically welded inner cylinder.
- The length of the inner cable guide and locking cylinder was not accurate, hence the locking was not happening.
- The tightening system needs to be worked with. It was too hard to tension the system.